Tableting Scale-Up Challenges
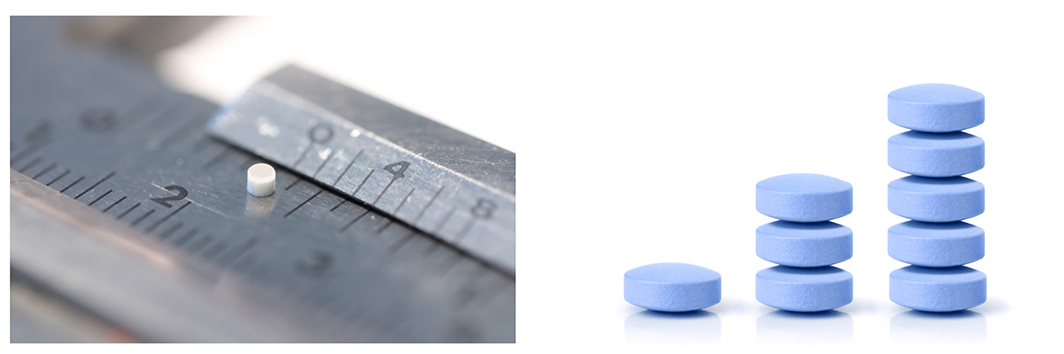
A focus of the last years was to generalize and determine critical quality attributes for the compression step and the final tablet parameters. Only recently (2017), at least at the scale of tablet compression development, the USP chapter <1062> Tablet Compression Characterization(*) was summarizing the newest standards. The following parameters are recommended to be investigated to gain deeper understanding of the formulation and its performance during compression:
8. MANUFACTURABILITY PROFILE*
9. TABLETABILITY PROFILE*
10. COMPRESSIBILITY PROFILE*
11. COMPACTIBILITY PROFILE*
12. TABLET COMPRESSION PROFILE*
13. MACHINE SPEED SENSITIVITY*
Guidance is given on how to perform the different profiles and which general considerations and requirements should be met. A tablet testing device as well as an instrumented tablet press are prerequisite equipment to assess tablet mechanical strength and porosity as well as punch displacement and compression force.
As explained earlier, formulation as well as final tablet properties can vary excessively. To incorporate a new formulation/ tablet into the general assessment and compare it to products which have proven to be successful within large scale production, normalization is key. Therefore, compression force should be translated into compression pressure and breaking force into tensile strength to be able to compare products with different punch format as well as tablet heights.
Within the Medelpharm-KORSCH portfolio, the compaction simulators STYL’One Evolution fulfill these prerequisites as punch displacement and compression force are measured with high precision even at high punch speeds. Also, the eccentric press XP 1 is equipped with precise displacement and force measurement and with the PharmaResearch® software, so that data can be collected, stored, and evaluated. Normalized values like compression pressure and tensile strength are automatically calculated for evaluation.
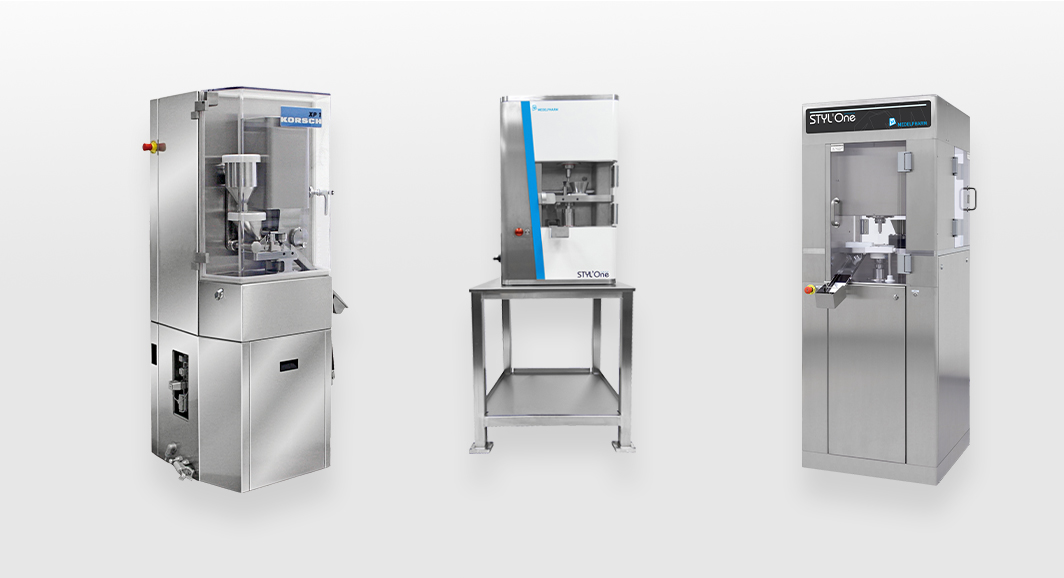
How to interpret the profiles is the challenging question. The USP monograph gives information about the commonly used parameter range but no real target values. In industry, certain target numbers evolved over the years like a target tablet tensile strength of 1.7 MPa or even better >2 MPa so that the tablets can withstand further processes like coating and/or packaging without facing issues. Still, the complex data interpretation with considering all important values should lay in the hand of experienced experts for getting a full picture as some values might be interesting for one formulation but not for another formulation/product.
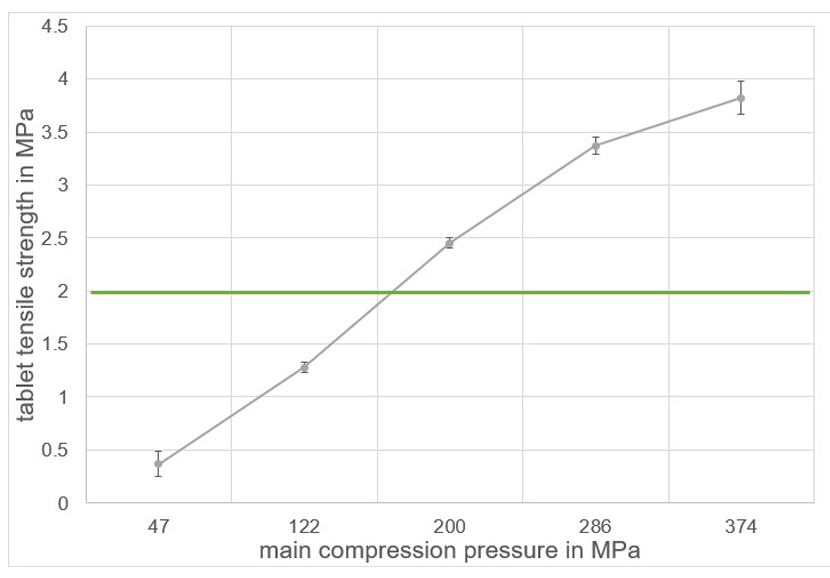
Medelpharm-KORSCH experts can help you with the data interpretation and give suggestions to your path forward as there is a unique combination of formulation scientists and process experts in place. If you already have a STYL’One compaction simulator, please have a look on mystylone.com and the published bulletins ‘’Why Tabletability Assessment Of Your Formulation Is A Fundamental Step of Your Tablet Development?’’ and ‘’QbD vs Troubleshooting’’ as here, the experts share their hands-on experience with you:
…The determination of the right material and quality attributes (e.g., lubrication, elasticity, cohesiveness, weight variation) can help in developing a robust formulation. An extensive characterization of a formulated blend can also prevent capping, sticking, or even die binding on an industrial-size rotary tablet press…
Transfer and scale-up a formulation from one tablet press to another can be a smooth process if the formulation has a wide design space meaning stable tablet quality attributes over a wide range of manufacturing set-ups like compression force and production speed. To compare different presses, calculations can be utilized. One example is the calculation of the consolidation time which is based on geometrical parameters such as radius of compression roller, radius of punch head flat, in-die tablet thickness, compression force and rate of total press deformation. Another widely used parameter is the dwell time which represents the portion of contact time when punches are not changing their vertical position in reference to the rollers. Minimum consolidation time and/or dwell time can be calculated to foresee the fastest possible production speed. Still, it has to be known at which consolidation time or dwell time tablets are produced within specification.
All above mentioned points/characterizations/calculations can only be assessed if the filling quality and quantity of the die is sufficient. It is the first point to address when it comes to scale-up or transfer of a product to another machine. If the filling is not sufficient, most tablet quality attributes will not match. So, why in literature and industry is this evaluation not performed to the same extent as the characterization of the compression itself? There are pharmacopoeia-based powder flow characterizations (like Hausner ratio or flow through an orifice) but linking their results to a flowability of the product into the die of a specific rotary press, isn’t generally possible yet. Powder interactions in the material supply and feeder of a tablet press are yet to be understood and to be characterized. In academia, various scientists investigate the filling process on linear filling devices with a moving feeder and a stationary die. Mathematical models are described to define the material flow into the die. Nevertheless, the transfer of those models on rotary presses was not overall successful. Again, the challenge is to normalize the powder and process parameters so that different formulations can be compared, and standards can be set. Schomberg et al. recently published their work about ‘’ Modeling gravity filling of dies on a rotary tablet press’’* utilizing the KORSCH XL 100. Tablet and powder properties (tablet weight and formulation bulk density) as well as press and process specific parameters (filling time, turret speed, paddle speed and filling height) were taken into account. A model was developed to calculate the critical paddle speed (for fully filled dies) solely with the determination of two powder characteristics: the formulation bulk density and powder bed permeability. The model was applicable to a variety of substances with different bulk densities and flow behavior within the press.
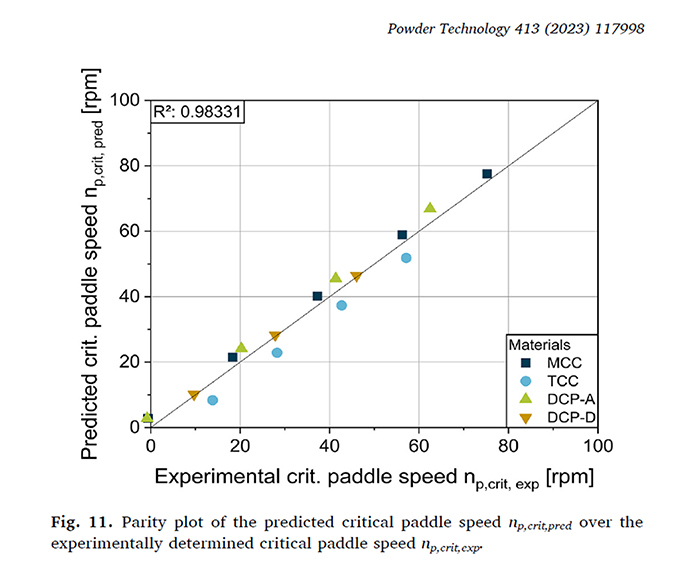
The question is: Can these new findings be used for a scale-up or a transfer to other or larger tablet presses? Investigations carried out at the INNOVATION CENTER by the Institute of Particle Technology at TU Braunschweig have shown that this is possible. Experiments were carried out on the KORSCH X 3 and XL 400 presses and have shown that die filling is based on the same mechanisms and follows similar trends. As a more important filling mechanism for the production of single-layer tablets, suction filling became the focus of more detailed investigations. In this case, the geometry of the filling curve is particularly decisive, as it ensures the pull-down of the lower punch and generates a negative pressure. What is even more industrially relevant is the extension of the model to two paddle feeders. This was done by considering specific geometric aspects of the feed frame and the fill cam, leading to accurate prediction of the filling performance. However, this data is not published yet so stay tuned for more information and upcoming publications.
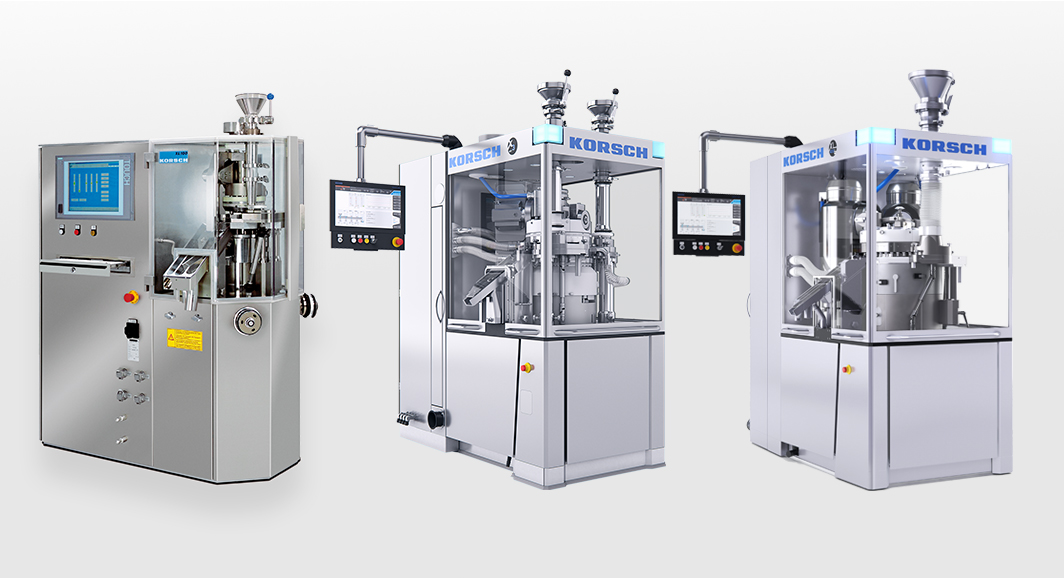
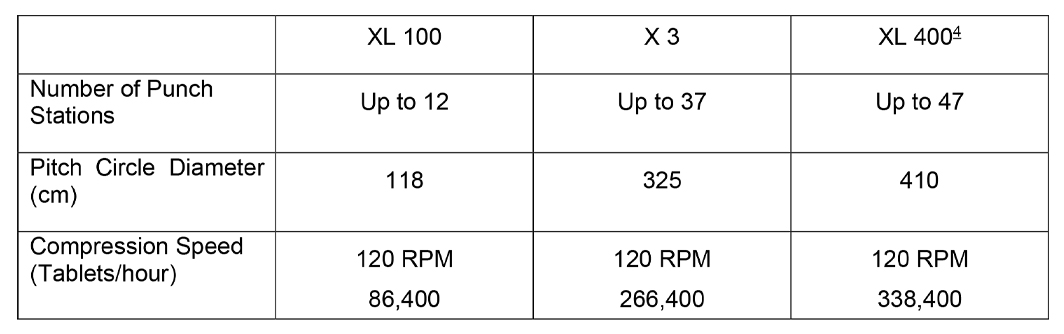
Nonetheless, for this model application, the powder flow must be sufficient to fill the die with a low filling volume variation. Filling issues occurring above the feeder were not taken into consideration. Therefore, the flowability of the formulation out of the bulk container, into the material supply and to the feeder must be assessed for each formulation and tablet press and is still not fully testable during formulation development. In literature some helps can be found like calculating the minimal outlet diameter of a container for a formulation considering its particle-particle-interaction properties. Also, the already mentioned pharmacopoeia monographs can give an indication for flowability levels. Unfortunately, the flowability within the tablet press is still the most challenging task found in compression trials in the INNOVATION CENTER Lab in Berlin. For more information and real-life examples, please see the KORSCH technology blog entry ‘’The critical role of product flow and die filling’’.
Summarized, considerable efforts are made to assess formulation properties at the level of formulation development to predict its performance during large scale production. Standards were set for some parameters but still a full prediction is not possible. KORSCH-Medelpharm and partners are continuously gaining new insights on scale-up predictability with their driven projects to fully support tablet production from small scale to large scale.
*A.K. Schomberg, A. Kwade, J.H. Finke, Modeling gravity filling of dies on a rotary tablet press, Powder Technology, Volume 413, 2023