Scale-Up in der Tablettierung: Eine Herausforderung
In den letzten Jahren ging es bei der Entwicklung von OSD vor allem darum, kritische Qualitätsmerkmale beim Pressvorgang zu verallgemeinern und endgültige Tablettenparameter zu bestimmen. Im Jahr 2017 veröffentlichte die USP ein offizielles Dokument (USP 1062) zur Charakterisierung der Tablettenkompression. In diesem Leitfaden wird empfohlen, zum besseren Verständnis der Formulierungen und ihrer Eigenschaften während des Pressvorgangs folgende Parameter zu untersuchen:
8. HERSTELLBARKEITSPROFIL*
9. TABLETTIERBARKEITSPROFIL*
10. KOMPRESSIBILITÄTSPROFIL*
11. KOMPAKTIERBARBEITSPROFIL*
12. TABLETTENKOMPRESSIONSPROFIL*
13. DREHZAHLEMPFINDLICHKEIT*
Es wird erläutert, wie die verschiedenen Druckprofile durchgeführt werden können und welche allgemeinen Überlegungen und Anforderungen zu beachten sind. Um die mechanische Festigkeit und Porosität der Tabletten sowie den Stempelweg und die Presskraft zu ermitteln, sind ein Tablettenprüfgerät und eine instrumentierte Tablettenpresse erforderlich.
Die Eigenschaften der Formulierung und der fertigen Tablette können sich je nach Anwendung erheblich unterscheiden. Um eine neue Formulierung/Tablette in die allgemeine Bewertung einzubeziehen und sie mit Produkten zu vergleichen, die sich in der Großproduktion bewährt haben, ist eine Normalisierung unerlässlich. Daher sollte die Presskraft in Pressdruck und die Bruchkraft in Bruchfestigkeit umgerechnet werden, damit Produkte mit unterschiedlichen Stempelformaten und Tablettenhöhen verglichen werden können.
Der Kompaktierungssimulator STYL'One Evo aus dem F&E-Produktportfolio von MEDELPHARM und KORSCH erfüllt diese Voraussetzungen, denn er misst Stempelweg und Presskraft auch bei hohen Stempeldrehzahlen sehr präzise. Auch die Exzenterpresse XP 1 ist mit einer präzisen Weg- und Kraftmessung sowie mit der PharmaResearch-Software ausgestattet, um Daten zu erfassen, zu speichern und auszuwerten. Für die Auswertung werden automatisch normalisierte Werte für Pressdruck und Bruchfestigkeit berechnet.
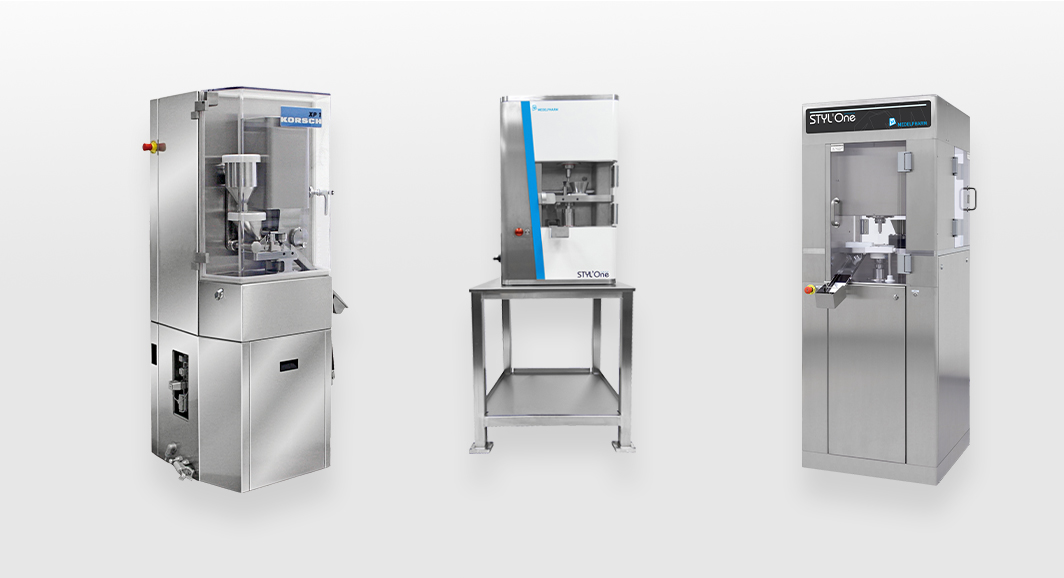
Die spannende Frage ist, wie die Druckprofile zu interpretieren sind. Die USP-Monografie gibt zwar Auskunft über die üblicherweise verwendeten Parameter, aber keine wirklichen Zielwerte. In der Industrie haben sich im Laufe der Jahre bestimmte Zielwerte herausgebildet, z. B. eine angestrebte Tablettenbruchfestigkeit von 1,7 MPa oder besser noch > 2 MPa als das Maß, bei dem die Tabletten weiteren Prozessen, einschließlich Beschichtung und Verpackung, standhalten können. Die komplexe Dateninterpretation, die alle relevanten Parameter berücksichtigt, erfordert jedoch immer noch viel Erfahrung und Fachwissen.
Im MEDELPHARM Science Lab in Lyon und im KORSCH INNOVATION CENTER in Berlin können unsere Formulierungs- und Prozessexperten bei der Materialcharakterisierung und vor allem bei der Interpretation der Daten helfen. Mit dem umfangreichen Geräteangebot, das ihnen dort zur Verfügung steht, unterstützen sie außerdem bei der Entwicklung und dem Scale-up. Für Kunden, die mit einem STYL'One-Kompaktierungssimulator arbeiten, stehen auf der MySTYL'One.com-Website hervorragende Artikel zur Verfügung, darunter "Warum die Bewertung der Tablettierfähigkeit Ihrer Formulierung ein grundlegender Schritt Ihrer Tablettenentwicklung ist" und "QbD vs. Troubleshooting".
Die Übertragung und das Scale-up einer Formulierung von einer Tablettenpresse auf eine andere können reibungslos vonstattengehen, wenn die Formulierung einen großen Design Space hat, d. h. die Qualitätsmerkmale der Tabletten sind in einem breiten Spektrum von Herstellungsparametern wie Presskraft und Produktionsdrehzahl stabil. Um verschiedene Pressen zu vergleichen, können Berechnungen herangezogen werden.
Ein Beispiel ist die Berechnung der Konsolidierungszeit, die auf geometrischen Parametern wie dem Radius der Druckrolle, dem Radius der Stempelkopffläche, der Tablettendicke in der Matrize, der Presskraft und der Gesamtverformungsrate der Presse beruht. Ein weiterer gängiger Parameter ist die Druckhaltezeit, die den Teil der Kontaktzeit darstellt, in dem die Ober- und Unterstempel ihre vertikale Position in Bezug auf die Druckrollen nicht verändern.
Die minimale Konsolidierungszeit und/oder Druckhaltezeit kann berechnet werden, um die schnellstmögliche Produktionsdrehzahl zu ermitteln. Es muss aber bekannt sein, bei welcher Konsolidierungszeit oder Druckhaltezeit Tabletten innerhalb der Spezifikationen hergestellt werden.
Die Presskraftparameter und die damit verbundenen Berechnungen können nur dann beurteilt werden, wenn die Füllqualität und -menge in der Matrize ausreichend sind. Dies ist der erste Punkt, der zu berücksichtigen ist, wenn es um das Scale-up oder die Übertragung eines Produkts auf eine andere Maschine geht. Wenn die Füllung nicht ausreichend ist, werden die meisten Qualitätsmerkmale der Tabletten nicht erreicht. Warum also wird diese Bewertung in der Literatur und in der Industrie nicht in gleichem Umfang vorgenommen wie die Charakterisierung des Pressvorgangs selbst?
Es gibt auf Pharmakopöen basierende Untersuchungen des Pulverflusses (wie das Hausner-Verhältnis oder der Fluss durch eine Blende), aber die Verknüpfung ihrer Ergebnisse mit der Fließfähigkeit des Produkts in die Matrize einer bestimmten Rundlaufpresse ist im Allgemeinen nicht möglich. Die Wechselwirkungen des Pulvers in der Materialzufuhr und im Füllschuh einer Tablettenpresse müssen erst noch verstanden und vollständig untersucht werden. Verschiedene Wissenschaftler an Hochschulen haben den Füllprozess an linearen Füllvorrichtungen mit beweglichem Füllschuh und feststehender Matrize untersucht. Die mathematischen Modelle, mit denen der Materialfluss in die Matrize definiert wurde, konnten jedoch in der Regel nicht auf Rundlaufpressen übertragen werden.
Auch hier liegt die Herausforderung darin, das Pulver und die Prozessparameter zu normalisieren, damit verschiedene Rezepturen verglichen und Standards festgelegt werden können. Schomberg et al. veröffentlichten kürzlich ihre Arbeit über die "Modellierung der Schwerkraftfüllung von Matrizen auf einer Rundlauftablettenpresse" , bei der die KORSCH XL 100 verwendet wurde. Dabei wurden Tabletten- und Pulvereigenschaften (Tablettengewicht und Schüttdichte der Formulierung) sowie pressen- und prozessspezifische Parameter (Füllzeit, Rotordrehzahl, Füllschuhdrehzahl und Füllhöhe) berücksichtigt.
Zur Berechnung der kritischen Füllschuhdrehzahl (bei vollständig gefüllten Matrizen) wurde ein Modell entwickelt, das ausschließlich auf der Bestimmung von zwei Pulvereigenschaften beruht: der Schüttdichte der Formulierung und der Durchlässigkeit des Pulverbettes. Das Modell war auf eine Vielzahl von Substanzen mit unterschiedlichen Schüttdichten und Fließverhalten in der Presse anwendbar.
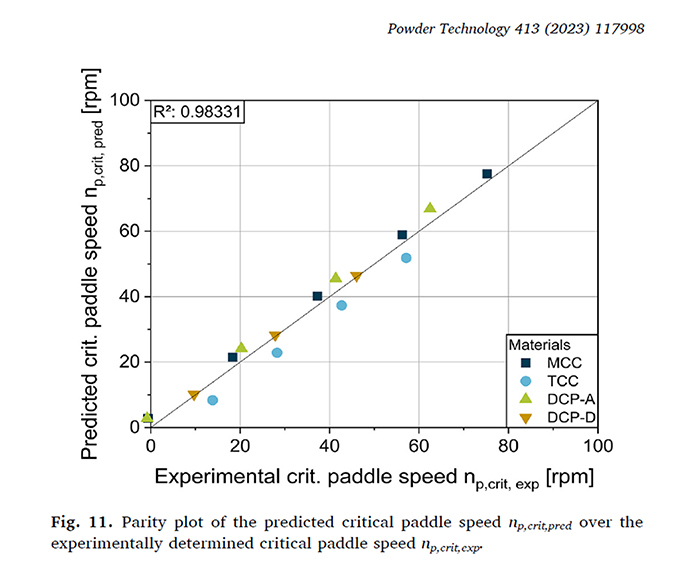
Die Frage ist: Können diese neuen Erkenntnisse für ein Scale-up oder eine Übertragung auf andere oder größere Tablettenpressen genutzt werden? Untersuchungen in unserem INNOVATION CENTER durch das Institut für Partikeltechnik der TU Braunschweig zeigten, dass dies möglich ist. Die Versuche wurden an den KORSCH Tablettenpressen X 3 und XL 400 durchgeführt und ergaben, dass die Matrizenfüllung auf den gleichen Mechanismen beruht und ähnlichen Trends folgt. Als Füllmechanismus, der für die Herstellung von Einschichttabletten von Bedeutung ist, rückte die Saugfüllung in den Mittelpunkt genauerer Untersuchungen. Hier war vor allem die Geometrie der Füllkurve entscheidend, da sie den Unterstempel herunterzieht und einen Unterdruck erzeugt. Von noch größerer Bedeutung für die Industrie war die Erweiterung des Modells auf zwei Füllschuhe mit Füllrädern. Dabei wurden spezifische geometrische Aspekte des Füllschuhgehäuses und der Füllkurve berücksichtigt, was zu einer genauen Vorhersage der Füllleistung führte. Da diese Daten jedoch noch nicht veröffentlicht sind, darf man auf weitere Informationen und künftige Veröffentlichungen gespannt sein.
Für diese Modellanwendung muss allerdings der Pulverdurchfluss ausreichen, um die Matrize mit geringer Füllvolumenschwankung zu füllen. Da Füllprobleme oberhalb des Füllschuhs nicht berücksichtigt wurden, muss die Fließfähigkeit der Formulierung aus dem Schüttgutbehälter oder IBC in die Materialzufuhr zum Füllschuh für jede Formulierung und Tablettenpresse bewertet werden. Dies ist im F&E-Maßstab nach wie vor schwierig.
In der Literatur finden sich einige Angaben dazu, wie der minimale Auslassdurchmesser eines Behälters für eine Formulierung zu berechnen ist, wobei die Eigenschaften der Partikel-Partikel-Wechselwirkung berücksichtigt werden. Auch die Monografien der Pharmakopöen können einen Hinweis auf die Fließfähigkeit geben. Leider ist die Fließfähigkeit auch bei Pressversuchen im INNOVATION CENTER in Berlin immer wieder ein Thema. Weitere Informationen und konkrete Anwendungsbeispiele finden Sie im KORSCH Technologie-Blog ''Die wichtige Rolle von Produktfluss und Matrizenfüllung''.
Insgesamt wurden erhebliche Anstrengungen unternommen, um die Eigenschaften von Formulierungen im F&E-Maßstab zu bewerten und für die großtechnische Produktion vorherzusagen. Auch wenn für einige Parameter Standards festgelegt wurden, ist eine vollständige Vorhersage nach wie vor nicht möglich. Mit verschiedenen Projekten, die die Tablettenproduktion vom Klein- bis zum Produktionsmaßstab optimal unterstützen, gewinnen KORSCH, MEDELPHARM und andere Partner dennoch kontinuierlich neue Erkenntnisse über die Vorhersagbarkeit des Scale-up.