Fließen und Füllen
Die Produktion kann grob in drei Schritte aufgeteilt werden.
- Füllung des Materials
- Kompaktierung des Materials zu einer Tablette
- Austragen dieser Tablette aus der Tablettiermaschine
Seitdem es Kompaktierungssimulatoren auf dem Markt gibt, kann der Schritt der Kompaktierung in kürzester Zeit und mit kleinsten Materialmengen untersucht werden. Nach der Kompaktierung erfolgt der Ausstoß der Tablette. Bei der Parametereinstellung der Kompaktierung sollte auch der Einfluss auf den Ausstoß der Tablette bedacht werden.
Die Füllung des Materials in die Matrizen ist zwar ein oft untersuchtes Thema, jedoch gibt es keinen Konsens über geeignete Tests, die die Fließeigenschaften in der Tablettiermaschine vorhersagen. Daher kann erst an der Tablettiermaschine selbst geprüft werden, wie gut sich das Material in die Matrizen füllen lässt und wie hoch die maximale Produktionsgeschwindigkeit ist. Um den Tablettierprozess also ökonomisch betreiben zu können, ist es essenziell, den Füllprozess zu verstehen und die Stellschrauben zu kennen.
Eine Möglichkeit, die Füllqualität zu beeinflussen, ist die Formulierungsentwicklung. Neben dem Arzneistoff finden sich meist viele weitere Hilfsstoffe in der Tablette: Binde-, Schmier- und Fließregulierungsmittel. Ein ausgewogenes Zusammenspiel der verschiedenen Komponenten kann zu einer guten Fließfähigkeit führen. Jedoch hat auch die chemische und physikalische Beschaffenheit der Komponenten einen großen Einfluss auf den Füllerfolg. Die Eigenschaften des Partikelhaufwerkes stehen hier im Vordergrund, denn Form, Größe und Oberflächenbeschaffenheit bestimmen die Interaktionen der Partikel untereinander und mit den produktberührenden Oberflächen der Tablettiermaschine.
Doch nicht nur eine Formulierungsanpassung kann zum gewünschten Erfolg einer schnellen Tablettierung mit hoher Gleichförmigkeit der Tablettenmasse führen. Auch die Füllsystemkonfiguration hat einen großen Einfluss auf die Füllung der Matrizen. Die einzelnen Komponenten können, angefangen von der Trichtergeometrie über die Oberflächenbeschaffenheit und Breite der Materialzuführung bis hin zur Füllschuh- und Füllradgeometrie die Gleichförmigkeit der Matrizenfüllung beeinflussen.
Die Füllzeit wirkt sich in den meisten Fällen am stärksten auf die Qualität der Matrizenfüllung und damit auf die Gleichförmigkeit der Tablettenmasse aus. Je nach Maschinenmodell und -konfiguration sind die Füllschuh- sowie die Füllkurvenlänge und damit die Füllstrecke vorgegeben. Aus den Füllstrecken können die Füllzeiten über die verschiedenen Produktionsgeschwindigkeiten errechnet werden.
Unterschiedliche Maschinenmodelle können unterschiedliche Materialzuführungsdurchmesser und Füllschuhgeometrien aufweisen. Die Fließfähigkeit ist also kein Faktor, der beim Produkttransfer auf eine andere Maschine einfach errechnet werden kann. Vielmehr spielt der Materialfluss vor und im Füllschuh eine entscheidende Rolle. Die Materialverteilung, die Scherkräfte, die auf das Material wirken, der Öffnungswinkel und die Öffnungsbreite zum Matrizentisch, die rückdosierte Pulvermenge und die Materialrückführung können die Füllung in die Matrize beeinflussen.
Am einfachsten ist der Effekt der Füllradgeometrie auf die Füllung zu testen. Bei jedem KORSCH Modell besteht die Möglichkeit, die Füllschuhräder auszutauschen. Dafür stehen diverse Geometrien zur Verfügung.
Doch wann sollte welches Füllrad eingesetzt werden? Auf diese Frage gibt es wegen der großen Variabilität und Freiheitsgrade in der Formulierung mit fast unendlichen Kombinationsmöglichkeiten leider keine einfache und eindeutige Antwort.
KORSCH konnte aber mit verschiedensten Kundenmaterialien und Maschinenmodellen umfangreiche Erfahrungen sammeln und übergeordnete Lösungsansätze erarbeiten. In diesem Artikel sollen einige Erfahrungswerte geteilt werden.
Die nachstehenden Daten wurden in Zusammenarbeit mit dem Institut für Partikeltechnik der TU-Braunschweig wissenschaftlich ermittelt. Im darauffolgenden Block werden Praxisbeispiele beschrieben, deren Daten im KORSCH INNOVATION CENTER in Berlin mit Kundenmaterial entstanden sind.
Wissenschaftlich ermittelte Daten zum Einsatz von Füllrädern
Füllräder können nach drei Kategorien unterschieden werden: Form, Anzahl und Höhe der Finger.
Um mögliche Unterschiede in der Fülleffizienz aufzuzeigen, wurden Bedingungen gewählt, die eine herausfordernde Füllaufgabe darstellten, wie z. B. eine große Fülltiefe mit nur sehr geringer Ausdosierung. Zwei Materialien mit unterschiedlichen Dichten und Partikelgrößen (und damit unterschiedlichem Fließverhalten) wurden ausgewählt.
Die Daten wurden mit gleicher Stempelgeometrie aufgenommen. Die vollständige Füllung der Matrizen lässt sich durch ein Plateau bei hohen Füllraddrehzahlen erkennen.
Die ermittelten Daten zeigen, dass Materialien, die eine gute Fließfähigkeit haben und nicht scherempfindlich sind mit allen genutzten Füllrädern gut in die Matrizen gefüllt werden können. Die Erhöhung der Füllradgeschwindigkeit hatte einen deutlich höheren Einfluss als die unterschiedlichen Füllrädergeometrien (Anzahl, Höhe und Form der Finger).
Bei Pulvern, die sich leicht verdichten lassen, hat die Füllradgeometrie einen hohen Stellenwert. Das genutzte Model-Material zeigte eine Verdichtung im Füllschuh und benötigte eine konstante, gleichmäßige Fließbewegung für eine ausreichende Füllung. Somit war hier das Füllrad mit großer Fingeranzahl vorteilhaft und eine gewissen Höhe sogar essenziell für eine Füllung der Matrizen.
Praxisbeispiele zur Verbesserung der Füllleistung durch geeignete Füllräder bei der Produktion von Mehrschichttabletten
Bei Pressversuchen im KORSCH INNOVATION CENTER in Berlin werden verschiedenste Produkte auf allen Maschinenmodellen verpresst. Viele Produkte sind bestehende Marktprodukte, während andere gerade im Entwicklungsprozess sind.
Besonders in der Produktion von Mehrschichttabletten können sich Herausforderungen zeigen. Der Füllprozess der ersten Schicht ist grundlegend anders als der Füllprozess der folgenden Schichten. Während der Füllung der ersten Schicht wird der Unterstempel über die Füllkurve herabgezogen, so dass ein Sogeffekt entsteht. Bei der Füllung der nachfolgenden Schichten kann das Pulver durch die bereits vorhandene erste Schicht nur gravimetrisch in die Matrize fallen. Die meist schlechtere Füllung auf der zweiten/dritten Schicht kann ein limitierender Faktor für die maximale Produktionsgeschwindigkeit sein.
Die untenstehenden drei Beispiele zeigen, dass die Geometrie der Rührflügel darüber entscheiden kann, ob eine Produktion erfolgreich ist oder nicht und dies abhängig von den Eigenschaften des Pulverhaufwerkes ist.
Beispiel 1 – Rührflügelgeometrie – Gleichmäßigkeit der Füllung
Das folgende Beispiel einer Zweischichttablettenproduktion zeigt, dass die Füllleistung durch geänderte Rührflügelgeometrien verbessert werden kann. Ein eckiges Füllrad führte zu einer gleichmäßigeren Füllung als ein rundes Füllrad. Die Unterschiede waren absolut gesehen nicht hoch, könnten jedoch für enge Tablettenspezifikationen entscheidend sein.
Zu sehen war auch, dass bei einem runden Füllrad die Drehzahl erhöht werden musste. Das Pulver wurde weniger aktiv in die Matrize gestrichen, sodass eine schnellere Bewegung zur gleichmäßigen Befüllung nötig war. Dieses Phänomen wird häufig im KORSCH INNOVATION CENTER beobachtet und ist nicht nur auf dieses Beispiel limitiert.
Beispiel 2 – Rührflügelgeometrie – Absolute Füllmenge
Das nächste Beispiel zeigt, dass sich die Gleichförmigkeit der Befüllung bei geänderter Füllradgeometrie nicht unbedingt ändern muss.
Beim obigen Beispiel ließ sich aber auch beobachten, dass die absolute Menge der Füllung mit runden Füllrädern erhöht werden konnte. Dies war bei Pulvern zu sehen, die leicht vorverdichteten und durch die Auflockerung der runden Füllräder eher zum Fließen in die Matrizenöffnung neigten.
Beispiel 3 – Rührflügelgeometrie- Relevanz
In seltenen Fällen bestimmt die Geometrie des Füllrades, ob überhaupt eine Produktion möglich ist oder nicht.
Bei folgendem Beispiel konnte die zweite Schicht bei einer Zweischichttablettenproduktion nicht mit rechteckigem Füllrad gefüllt werden. Bei hohen Füllraddrehzahlen wurde das Pulver im Füllschuh verdichtet, so dass der Füllradantriebsmotor den maximal möglichen Widerstand erreichte und die Presse automatisch gestoppt wurde. Bei niedrigen bis mittleren Füllraddrehzahlen wurde die Matrize nicht vollständig gefüllt. Sobald das Füllrad getauscht wurde, konnte bei der Zielgeschwindigkeit kontinuierlich und innerhalb der Spezifikation produziert werden.
Ermittlung der geeigneten Maschinenkonfiguration bei der Produktion von Mehrschichttabletten
Neben der Rührflügelgeometrie kann auch die Maschinenkonfiguration eine große Rolle bei der Produktion von Mehrschichttabletten spielen. Die Plattform der XL 4004 MFP bietet die Möglichkeit, zwischen verschiedenen Füllstrecken für die jeweiligen Schichten zu wählen.
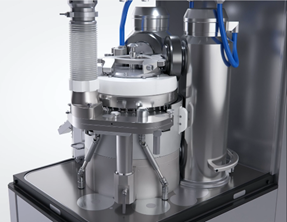
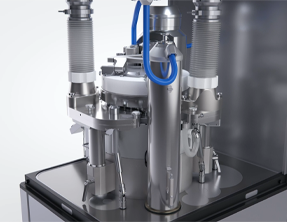
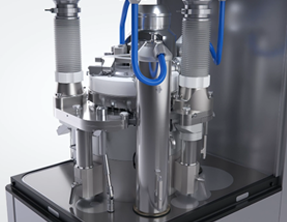

Beispiel 1 - Füllstrecke
Bei folgendem Beispiel sollte die optimale Maschinenkonfiguration für das Kundenprodukt ermittelt werden. Mit einer langen Füllstrecke auf der ersten Schicht und einer langen Füllstrecke auf der zweiten Schicht konnte die Maschine mit einer hohen Rotordrehzahl gefahren werden. Der Aufbau weiterer Konfigurationen zeigte, dass die lange Füllstrecke für eine gleichförmige Füllung auf der ersten Schicht sehr wichtig war, da die relative Standardabweichung sprunghaft stieg, wenn die kürzere Füllstrecke auf der ersten Schicht gewählt wurde.
Beispiel 2 – Art der Füllung
Bei einer festgelegten Konfiguration wie z. B. bei der XT 600 kann die Schichtreihenfolge entscheidend sein. Alle pulverförmigen Produkte profitieren vom Sogeffekt der Füllkurve auf der ersten Schicht. Für manche Produkte ist dieser jedoch essenzieller als für andere Produkte.
Das untenstehende Praxisbeispiel zeigte, wie die schon gute relative Standardabweichung der Tablettenmasse von 1,43 % der ersten Schicht noch auf 0,43 % reduziert werden konnte. Die Schichten wurden bei sonst gleichen Produktionsparametern getauscht. In diesem Fall verbesserte sich ebenfalls die Gleichförmigkeit der Füllung auch auf der zweiten Schicht.
Fazit
Die Praxisbeispiele zeigen, dass es Pulverhaufwerke gibt, die eine Herausforderung für den Füllprozess von Matrizen darstellen. Hierzu zählen unter anderem Pulver mit schlechter Fließfähigkeit, Pulver, die leicht verdichtet werden können, und Pulver mit geringer Schüttdichte (große Pulvervolumina, die gefüllt werden müssen).
Diese Herausforderung kann jedoch mit einem modularen Füllsystem und einer optimierten Prozesseinstellung - in den meisten Fällen ohne Formulierungsanpassung - überwunden werden. Da Pulvermischungen und deren Interaktion sowohl untereinander als auch mit den Maschinenbauteilen sehr komplex sind, muss die Fließfähigkeit im System Tablettiermaschine bei den gewünschten Zielparametern untersucht und ggf. angepasst werden.
KORSCH kann hier mit langjähriger Erfahrung unterstützen und zur Entwicklung eines ökonomischen und stabilen Tablettierprozesses beitragen.